[Download] AIS Lab - Free SW - A2C (Accelerometer Auto Calibration)
[Download]
Accelerometer Auto Calibration (A2C) - abstract
Up to now, little attention has been posed on a
principled derivation of the cost function used for autocalibration of
MEMS
triaxial accelerometers [1], [2]. Here we formulate the
calibration problem in the context of maximum
likelihood and we derive a general formulation that can be
reduced
to the classical quadratic cost function under certain hypotheses. We
also use the Akaike Information Criterion to automatically determine the
most
adequate linear sensor model for the given calibration data set.
The adopted accelerometer model is linear and it is described as [1 - 4]:
vn = VCC (Sa-o) + n (1),
where vn is the noisy output of the sensor (including the X, Y and Z channel), VCC is the supply voltage, S is a 3x3 sensitivity matrix, a is the acceleration sensed by the accelerometer, o is the offset vector and n is the noise vector, which is assumed to be Gaussian. Sensor calibration consists in a procedure to estimate S and o from a set of measured data, such that Eq. (1) can be inverted and the acceleration a can be properly estimated.
Autocalibration is performed by minimization of a properly defined cost
function. This is derived from the sensor model in Eq. (1) in the
context of maximum likelihood estimate and considering that, in static
condition, the module of the acceleration measured by the accelerometer
is equal to g [1 - 4]. Considering N different sensor orientations, the
following cost function can be considered:
F = sumi=1..N[ (vn,i /VCC - o)T S-T S-1 (vn,i /VCC - o) - g2 ]2 (2),
where vn,i
represents the noisy output of the sensor in the i-th orientation.
Minimization of F in Eq. (2) is performed by means of the
Levemberg-Marquardt method, and it leads to the estimate of S and o.
Depending on the number of free elements in S and o
in Eq. (1), sensor models with 2, 6, 9 or 12 parameters can be
considered. In the proposed method, calibration is performed for each
of these models; selection is the best model is then performed by means
of the Akaike criterion, properly corrected to take into account
the bias introduced by small dataset [1].
A large set of calibration results is presented in [1]. Here experiments on
both simulated and real data show the effectiveness of the proposed
approach, which guarantees higher accuracy with respect to more
traditional calibration techniques like those in [2 - 4].
Free SW - Download and instruction
Libraries used
This software makes use of QT libraries dll (http://qt.nokia.com/products/)
for the user interface, that is distributed by Nokia under LGPL licence.
Download
From here, you can download a compressed .rar
file including a free copy of an executable (.exe) file which runs under Win
32 Platform (if you are interested in code compiled for different operative
systems, please contact directly the authors by e-mail). In the same file, you'll
find some calibration dataset too.
Instruction - installation
The executable file (and necessary DLLs) are all included in the compressed
file. To install them, just decompress the .rar file in your directory. Then,
to run A2C, just double
click on A2C.exe.
Instruction - use of the A2C
To calibrate an accelerometer, you have to position it in N random orientation.
For each orientation you have to measure the output of the accelerometer (in
Volts) and save it in a text file with N rows and 3 columns; the i-th row of
the text file will contain the X, Y and Z output of the accelerometer for the
i-th orientation. Once you have created the file, you are ready to calibrate
the accelerometer with A2C.
Double click on A2C.exe. and the following GUI will appear:
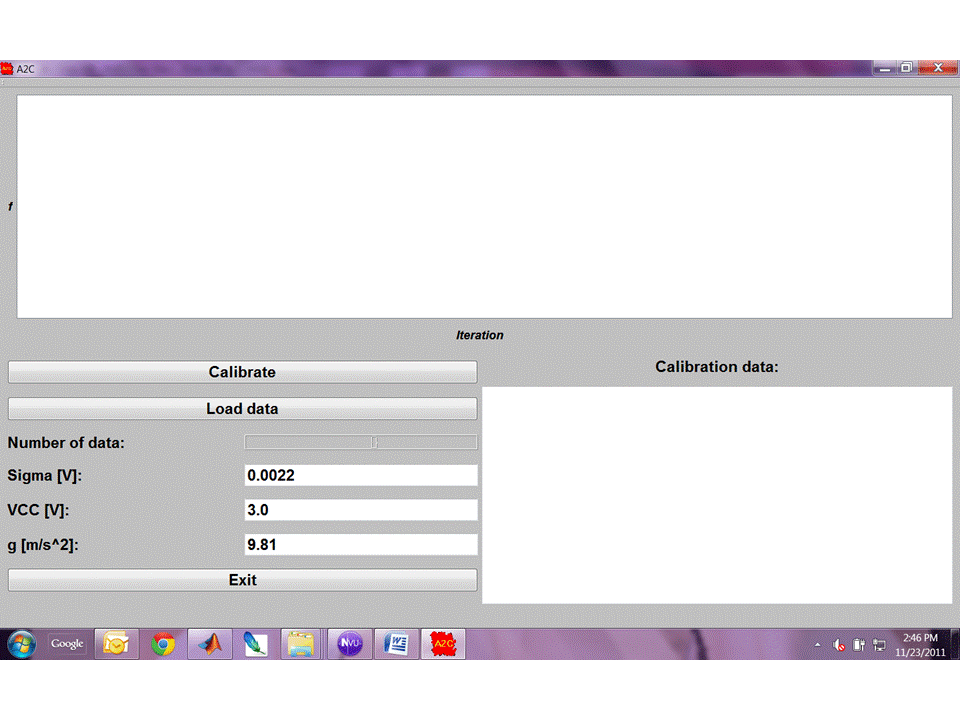
In this GUI, you have to
insert the voltage supply (VCC [V]), the noise standard deviation on each channel
of the accelerometer (taken from it datasheet, in Volt - Sigma [V]) and the
value of g. Then, load the data using the "Load data" button and indicating
the text file with the accelerometer data and push the "Calibrate" button to
calibrate the sensor.
Calibration is performed for sensor models with 2, 6, 9 and 12 parameters. Then,
the best model is selected by the Akaike Information Criterion and the GUI appear
as:
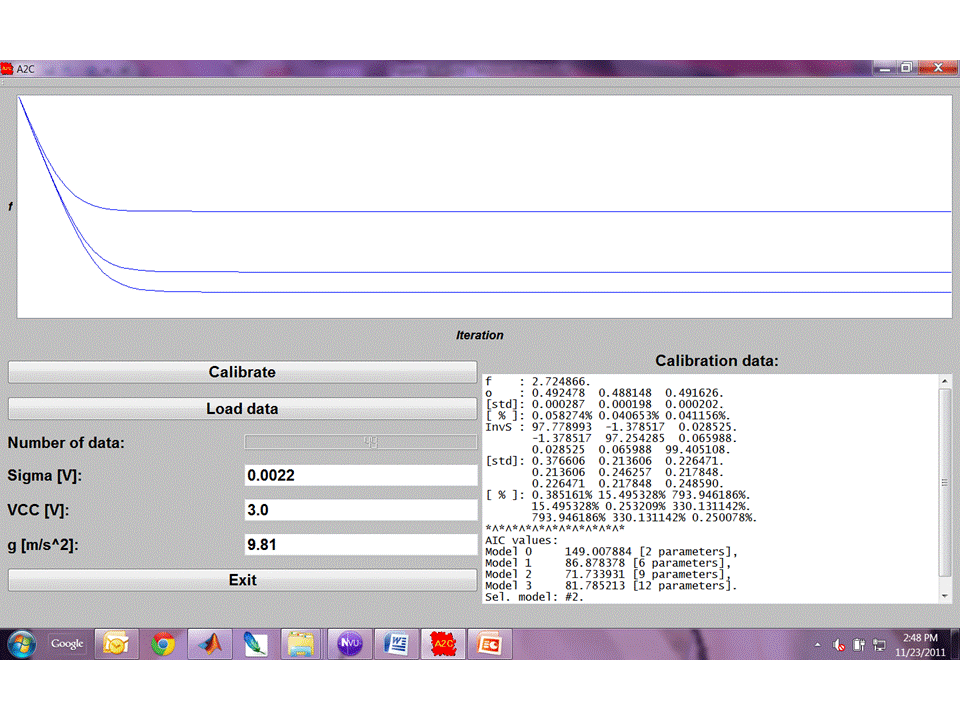
In the upper panel, the cost function as a function of the iteration is plotted
for all the sensor models considered. In the lower panel on the right, calibration
data are displayed. More in detail, you can observe the value of the cost function
f for the best model selected and the values of o
and S-1
(InvS) for the same model. For each component of o
and S-1it
is also shown the accuracy on the parameter, estimated by means of the covariance
analysis; the corresponding percentage confidence of the parameter is also reported.
Finally, the AIC indexes for the four models considered are also reported in
this panel.
In the same directory of A2C.exe, you will also find a set of log files, that
contain information on the estimated parameters for each sensor model considered
by the present method.
Contact and other information
For any information, please contact:
Iuri Frosio, PhD
Computer Science Dept.
University of Milan
Via Comelico 39/41
+39 02 503 14010
frosio@dsi.unimi.it
THE SOFTWARE IS PROVIDED "AS IS", WITHOUT WARRANTY OF ANY KIND.
If you are using the SW for scientific use, please cite our work [1].
If you are interested in the commercial use of the SW, please contact the authors.
References
[1]
I. Frosio, F. Pedersini, N. A. Borghese, Autocalibration of MEMS
Accelerometers with Automatic Model Selection, IEEE Sensors Journal, in
print.
[2] I.
Frosio, F. Pedersini, N. A. Borghese, Autocalibration of MEMS
accelerometers, to appear in Advanced Mechatronics and MEMS Device,
Edited by: Dan Zhang, Springer, 2011.
[3] I.
Frosio, F. Pedersini, N. A. Borghese, "Autocalibration of MEMS
Accelerometers," IEEE Transactions on Instrumentation and
Measurements,Vol. 58, No. 6, Jun. 2009, pp. 2034-41.
[4] I.
Frosio, S. Stuani, N. A. Borghese, Autocalibration of MEMS
accelerometer, in Proc. IMTC 2006, Sorrento (Italy), 25-27 April 2006.